Advanced logistics services
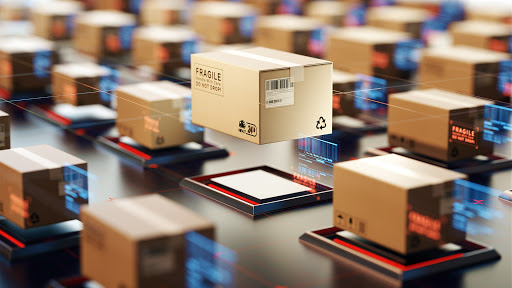
Logistics and distribution are some of the key processes that, when made efficient, provide the perfect shopping experience for consumers.
Today, for logistics operators, advanced services to support the supply chain are the focal point on which to concentrate in order to be competitive on the market and at the same time to generate value for the customer who decides to undertake an ad hoc logistics project.
Before going into detail, it is worth defining what is meant by advanced logistics services: these are activities outside the traditional logistics process that, in most cases, are managed directly by clients. The offer of such services by logistics operators identifies a way to expand and improve the market dimension, while at the same time generating value-added services for customers. Logistics and distribution are some of the main processes that, if made efficient, allow to offer consumers the perfect shopping experience.
Technological innovation, therefore, can be applied to both traditional and advanced services. The biggest change, however, is in the innovation of traditional services, which have evolved, increasingly responding to customer needs.
In order to be able to analyse the main changes in logistics warehouses in detail, we can use Porter’s value chain (M.Porter, 1985) as a basis. Value creation means the creation of a benefit for both the company and the end consumer. The product must be able to generate a benefit not only for the company, which thus succeeds in destabilising its competitors, but also for the end customer, who is able to satisfy a need by purchasing a particular product.
In the value chain, so-called primary activities can be identified; each of them increases the value of what is offered or of what is produced/processed and, all together, they determine the advantage that the company is able to generate thanks to the organised efforts it puts in place:
- production of goods and services/ operations
- inbound logistics
- outbound logistics
- customer service
- marketing and sales
The changes are significant and, for this reason, it is worth analysing them one by one to fully understand the particular value they could bring to Vendors:
Inbound logistics and production are undergoing significant changes due to recent technological innovations. First and foremost is the supply of production systems. In this area, there are several innovative solutions that allow warehouses and assembly stations to be supplied according to the production plan. What could happen in some cases is the creation of sequenced containers or kits containing all the components needed for assembly or pre-assembly within the warehouses; these kits will then be transported to the customer’s plant and allow better management of time and the entire logistics process. In production, there are some logistics service providers who intervene directly in certain stages of the production process and thus provide the vendor with added value that saves time and money.
Outbound logistics is innovated by the assembly, configuration and customisation of the product by the logistics service provider. Examples include the configuration of software updates for a consumer electronics manufacturer directly in the warehouse before shipping the products, or the installation of hard disks in the product according to the target market and the customer’s chosen configuration, thereby optimising the process from a customs point of view. Another important factor is the customisation of packaging, which is carried out directly by the logistics supplier who is able to carry out the palletisation and customisation process. The packaging is in fact modified according to the configuration of the goods and the needs of the vendor. In this way, the logistics service provider manages the entire packaging development and production process, from design through to procurement and implementation.
Integrated after sales and customer service: This represents the development by the logistics service provider of a proactive customer service system to which the end customer turns for both logistics-related and product-related service issues. In this way, the logistics provider operates with a single interface, connecting the points of sale on behalf of customers and responding directly to messages and calls sent to customer service.
Logistics for the circular economy: this is an important process that is represented by the involvement of the logistics service provider in the management of returns (transport, storage, quality control) and their recovery, reconditioning and/or re-introduction into the market, as well as in the disposal of non-recoverable products. For example, some logistics operators collect returns from both traditional and eCommerce sales channels, carry out quality control, classification and, if necessary, reconditioning, and return to the customer pallets already prepared for the various valorisation channels.
The development of advanced services will therefore become an increasingly important scenario for logistics service providers. There is and will be a greater involvement of these players in all phases of the transformation of goods, as they represent a significant support point when the end customer requires increasingly customised products and services. Companies, with the help of their logistics partners, will therefore have to reshape themselves and increasingly adapt to the external environment in order to offer their customers a service tailored to their needs.